System wentylacji przemysłowej, a w szczególności okap przemysłowy, stanowi serce każdej profesjonalnej kuchni czy zakładu produkcyjnego, gdzie procesy technologiczne generują ciepło, parę wodną, dym, tłuszcze i zapachy. Podstawową rolą okapy przemysłowego jest zapewnienie bezpiecznego, higienicznego i komfortowego środowiska pracy poprzez skuteczne usuwanie zanieczyszczeń. Jednakże, tradycyjne systemy wentylacyjne, często pracujące ze stałą, maksymalną wydajnością niezależnie od rzeczywistego obciążenia, stają się znaczącym źródłem kosztów operacyjnych. Zużywają one duże ilości energii elektrycznej do napędu wentylatorów oraz, co równie istotne, generują koszty związane z ogrzewaniem lub chłodzeniem powietrza uzupełniającego, które musi zastąpić usunięte powietrze z pomieszczenia.
W obliczu rosnących cen energii, coraz bardziej rygorystycznych przepisów dotyczących efektywności energetycznej i emisji, a także rosnącej świadomości ekologicznej, optymalizacja systemów wentylacji przemysłowej przestaje być jedynie opcją, a staje się koniecznością. Optymalizacja ta przynosi wymierne korzyści na wielu płaszczyznach: znacząco redukuje koszty eksploatacyjne, minimalizuje negatywny wpływ działalności na środowisko naturalne, poprawia komfort pracy personelu poprzez redukcję hałasu i zapewnienie stabilniejszych warunków termicznych, a także pomaga w spełnieniu lub nawet przekroczeniu obowiązujących norm i regulacji.
Niniejszy artykuł stanowi rozwinięcie i uzupełnienie podstawowego przewodnika po okapach przemysłowych, skupiając się na zaawansowanych metodach i technologiach służących optymalizacji ich pracy. Zagłębimy się w kluczowe aspekty efektywności energetycznej, przedstawiając konkretne rozwiązania technologiczne pozwalające na racjonalne gospodarowanie energią. Szczegółowo omówimy rewolucyjne systemy inteligentnego sterowania, znane jako Wentylacja Sterowana Zapotrzebowaniem (Demand Control Kitchen Ventilation – DCKV), które dynamicznie dostosowują pracę systemu do aktualnych potrzeb. Przyjrzymy się również nowoczesnym technologiom filtracji, takim jak filtry elektrostatyczne (ESP) i systemy wykorzystujące promieniowanie UV-C, które nie tylko skutecznie oczyszczają powietrze, ale również przyczyniają się do zwiększenia bezpieczeństwa i uproszczenia konserwacji.
Nowoczesne systemy wentylacji przemysłowej stanowią fundament efektywności energetycznej i bezpieczeństwa w obiektach gastronomicznych, hotelowych oraz zakładach produkcyjnych. Rosnące wymagania dotyczące jakości powietrza, przy jednoczesnej presji na optymalizację kosztów operacyjnych, stawiają przed właścicielami i zarządcami tych obiektów poważne wyzwania. Rozpoznanie dostępnych możliwości technologicznych, zrozumienie ich potencjału oraz umiejętność wyboru rozwiązań najbardziej odpowiednich do konkretnych warunków stają się kluczowymi kompetencjami dla każdego, kto planuje inwestycję lub modernizację systemu wentylacyjnego.
Odpowiednio zaprojektowane i zoptymalizowane instalacje nie tylko zapewniają komfort użytkownikom, ale przede wszystkim pozwalają na znaczące oszczędności energii, redukcję kosztów eksploatacji oraz zmniejszenie negatywnego wpływu na środowisko.
Efektywność Energetyczna: Klucz do Redukcji Kosztów
Tradycyjne systemy wentylacji przemysłowej, działające często w trybie „włącz/wyłącz” lub ze stałą, maksymalną wydajnością, są jednymi z największych konsumentów energii w obiektach gastronomicznych i przemysłowych. Analiza struktury zużycia energii w tych systemach ujawnia dwa główne obszary, w których tkwi największy potencjał oszczędności: energia elektryczna zużywana przez wentylatory wyciągowe i nawiewne oraz energia cieplna (lub chłodnicza) potrzebna do obróbki (ogrzania zimą, schłodzenia latem) powietrza uzupełniającego, które musi zostać wprowadzone do pomieszczenia w miejsce usuniętego powietrza.
Na szczęście, postęp technologiczny w dziedzinie HVAC oferuje szereg rozwiązań pozwalających na znaczące zwiększenie efektywności energetycznej systemów wentylacji przemysłowej. Inwestycja w te technologie, choć początkowo może wydawać się kosztowna, w perspektywie długoterminowej przynosi znaczące oszczędności operacyjne i szybszy zwrot poniesionych nakładów.
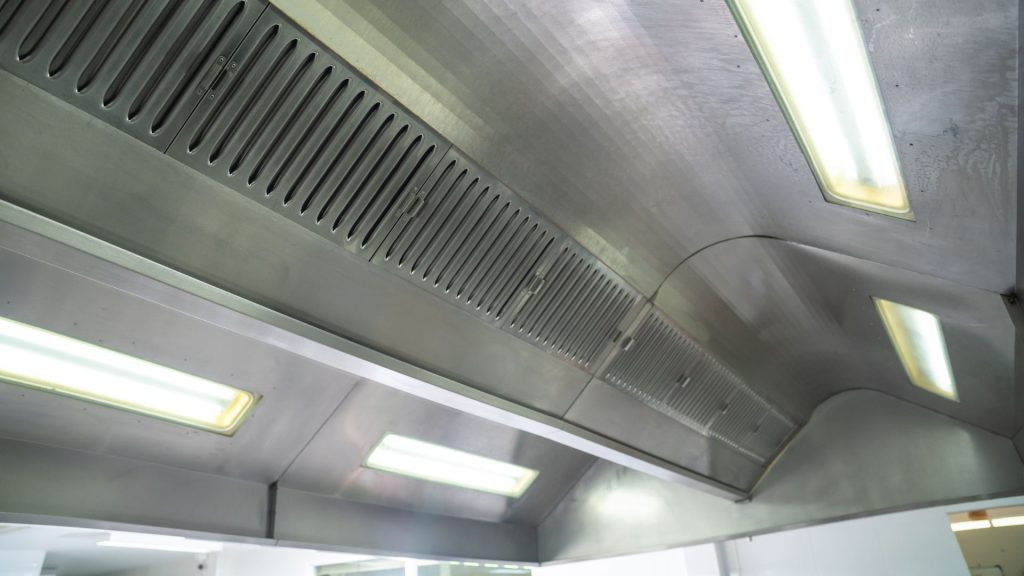
Technologie i Strategie Oszczędzania Energii
Kluczem do efektywności energetycznej jest inteligentne zarządzanie przepływem powietrza i minimalizowanie strat energii. Oto najważniejsze technologie i strategie:
- Wentylatory o Wysokiej Sprawności: Serce każdego systemu wentylacyjnego stanowią wentylatory. Zastąpienie starszych modeli wentylatorów z tradycyjnymi silnikami prądu przemiennego (AC) nowoczesnymi wentylatorami wyposażonymi w silniki EC (Electronically Commutated) to jeden z podstawowych kroków ku oszczędności.
Silniki EC charakteryzują się znacznie wyższą sprawnością, szczególnie przy częściowym obciążeniu, cichszą pracą oraz możliwością precyzyjnej regulacji prędkości obrotowej bez konieczności stosowania dodatkowych, często skomplikowanych i drogich, regulatorów. - Napędy o Zmiennej Prędkości (VSD/VFD): Nawet w przypadku stosowania wentylatorów z silnikami AC, zastosowanie przemienników częstotliwości (Variable Speed Drives – VSD lub Variable Frequency Drives – VFD) pozwala na płynną regulację prędkości obrotowej wentylatorów. Zgodnie z prawami fizyki dotyczącymi pracy wentylatorów, nawet niewielkie zmniejszenie prędkości obrotowej prowadzi do znaczącej redukcji zużycia energii (zależność sześcienna: zmniejszenie prędkości o 20% może zredukować zużycie energii nawet o 50%). VSD umożliwiają precyzyjne dopasowanie wydajności wentylacji do aktualnego zapotrzebowania, co jest szczególnie istotne w obiektach o zmiennym obciążeniu, jak restauracje.
- Systemy Wentylacji Sterowane Zapotrzebowaniem (DCKV): To najbardziej zaawansowane podejście do optymalizacji pracy wentylacji. Jak wskazują badania1 i dane rynkowe2, systemy DCKV mogą przynieść oszczędności energii sięgające nawet 50-70% w porównaniu do systemów o stałej wydajności. Ich działanie opiera się na ciągłym monitorowaniu warunków w strefie gotowania za pomocą czujników i dynamicznym dostosowywaniu prędkości wentylatorów (zarówno wyciągowych, jak i nawiewnych) do rzeczywistego zapotrzebowania. Temat ten zostanie szczegółowo rozwinięty w kolejnym rozdziale.
- Odzysk Ciepła (Rekuperacja): Powietrze usuwane z kuchni przemysłowej, mimo że zanieczyszczone, niesie ze sobą znaczną ilość energii cieplnej. Systemy odzysku ciepła (rekuperatory) pozwalają na odzyskanie części tej energii i wykorzystanie jej do wstępnego ogrzania (zimą) lub schłodzenia (latem, jeśli system jest odwracalny) świeżego powietrza nawiewanego do pomieszczenia. Stanowi to ogromny potencjał oszczędności na kosztach ogrzewania i klimatyzacji. Wyzwaniem w kuchniach przemysłowych jest obecność tłuszczu w powietrzu wyciągowym, który może osadzać się na wymienniku ciepła, zmniejszając jego efektywność i stwarzając ryzyko pożarowe. Dlatego stosuje się specjalne konstrukcje rekuperatorów (np. z wymiennikami krzyżowymi, obrotowymi o specjalnej konstrukcji, czy systemy z czynnikiem pośredniczącym), często wyposażone w dodatkowe systemy filtracji lub mycia wymiennika.
Rola Projektu, Wymiarowania i Konserwacji
Nawet najbardziej zaawansowane technologie nie przyniosą oczekiwanych rezultatów, jeśli system wentylacyjny nie zostanie prawidłowo zaprojektowany i zwymiarowany. Profesjonalny projekt, uwzględniający specyfikę obiektu, rodzaj i rozmieszczenie urządzeń generujących zanieczyszczenia, a także obowiązujące normy i przepisy, jest fundamentem efektywnego i bezpiecznego systemu. Niewłaściwe zwymiarowanie okapów, kanałów czy wentylatorów może prowadzić do nieefektywnego usuwania zanieczyszczeń, nadmiernego hałasu lub niepotrzebnie wysokiego zużycia energii.
Kluczowe znaczenie dla utrzymania wysokiej efektywności energetycznej przez cały okres eksploatacji systemu ma również regularna i prawidłowa konserwacja. Zaniedbania w tym zakresie prowadzą do stopniowego pogarszania się parametrów pracy systemu i wzrostu zużycia energii. Należy pamiętać o:
- Regularnym czyszczeniu lub wymianie filtrów: Zanieczyszczone filtry (przeciwtłuszczowe, wstępne, końcowe) stawiają większy opór przepływowi powietrza, zmuszając wentylatory do intensywniejszej pracy i zużywania większej ilości energii.
- Kontroli stanu wentylatorów: Sprawdzanie czystości wirników, stanu łożysk i pasków napędowych (jeśli występują).
- Sprawdzaniu szczelności kanałów wentylacyjnych: Nieszczelności powodują niekontrolowany napływ lub wypływ powietrza, zmniejszając efektywność systemu i zwiększając straty energii.
- Kontroli i kalibracji elementów sterujących: Regularne sprawdzanie działania czujników, przemienników częstotliwości i innych elementów automatyki.
Podsumowując, efektywność energetyczna systemów wentylacji przemysłowej to obszar o ogromnym potencjale optymalizacji. Świadomy dobór nowoczesnych technologii, profesjonalny projekt oraz regularna konserwacja pozwalają na znaczące obniżenie kosztów eksploatacyjnych, przy jednoczesnym zapewnieniu optymalnych warunków pracy i minimalizacji wpływu na środowisko.
Inteligentne Sterowanie: Przyszłość Wentylacji (Focus on DCKV)
Przełomem w dziedzinie optymalizacji wentylacji przemysłowej, szczególnie w kuchniach komercyjnych, okazały się Systemy Wentylacji Sterowane Zapotrzebowaniem (Demand Control Kitchen Ventilation – DCKV). Stanowią one inteligentną odpowiedź na marnotrawstwo energii związane z pracą tradycyjnych systemów wentylacyjnych ze stałą wydajnością. Zamiast utrzymywać maksymalny przepływ powietrza przez cały czas pracy kuchni, systemy DCKV dynamicznie dostosowują intensywność wentylacji do rzeczywistych potrzeb, wynikających z aktualnie prowadzonej aktywności kulinarnej. Jak potwierdzają liczne badania i dane producentów (np. Gaylord Ventilation, Halton, Energy Star), potencjał oszczędności energii dzięki wdrożeniu DCKV jest ogromny, często sięgając 50-70% w porównaniu do standardowych rozwiązań.
Zasada Działania Systemów DCKV
Sercem systemów DCKV jest zaawansowana technologia sensoryczna połączona z inteligentnymi algorytmami sterowania i elementami wykonawczymi w postaci wentylatorów z płynną regulacją prędkości (najczęściej poprzez VSD/VFD lub z wykorzystaniem silników EC). System w czasie rzeczywistym monitoruje warunki panujące w strefie gotowania pod okapem i na tej podstawie podejmuje decyzje o wymaganym w danym momencie przepływie powietrza wyciągowego i nawiewnego.
Technologie Sensoryczne: Kluczową rolę odgrywają czujniki, które dostarczają informacji o poziomie aktywności kulinarnej. Najczęściej stosowane są:
- Czujniki Temperatury: Monitorują temperaturę powietrza wyciąganego spod okapu lub bezpośrednio nad urządzeniami grzewczymi. Nagły wzrost temperatury jest sygnałem rozpoczęcia lub intensyfikacji procesu gotowania.
- Czujniki Optyczne/Podczerwieni (IR): Wykrywają obecność płomienia, gorących powierzchni lub pary wodnej i dymu, bezpośrednio wskazując na aktywność urządzeń kuchennych. Są one często bardziej precyzyjne i szybsze w reakcji niż czujniki temperatury.
- Czujniki Dymu/Pary: Specjalistyczne czujniki dedykowane do wykrywania cząstek stałych (dymu) lub wysokiej wilgotności (pary).
Zaawansowane systemy często wykorzystują kombinację różnych typów czujników (np. temperaturę i IR), aby zwiększyć niezawodność i precyzję detekcji różnych faz procesu gotowania (urządzenie włączone, w stanie gotowości, intensywne gotowanie/smażenie).
Algorytmy Sterowania: Dane z czujników są przetwarzane przez sterownik systemu DCKV, który na podstawie zaprogramowanych algorytmów określa wymagany poziom wentylacji. Algorytmy te uwzględniają typ urządzeń kuchennych, ich moc, a także specyfikę procesów (np. smażenie generuje więcej zanieczyszczeń niż gotowanie na parze). System płynnie reguluje prędkość obrotową wentylatorów wyciągowych, aby zapewnić odpowiedni przepływ powietrza do wychwycenia zanieczyszczeń. Jednocześnie, aby utrzymać zbilansowane ciśnienie w pomieszczeniu, system steruje również wentylatorami nawiewnymi, dostarczając odpowiednią ilość powietrza uzupełniającego.
Kluczowe Korzyści z Wdrożenia DCKV
Implementacja systemu DCKV przynosi szereg wymiernych korzyści:
- Maksymalizacja Oszczędności Energii: To podstawowa zaleta. Redukcja przepływu powietrza w okresach braku lub niskiej aktywności kulinarnej (np. między posiłkami, podczas przygotowań wstępnych) prowadzi do drastycznego obniżenia zużycia energii przez wentylatory (zależność sześcienna). Równie istotne są oszczędności wynikające ze zmniejszonej potrzeby ogrzewania lub chłodzenia powietrza uzupełniającego – im mniej powietrza usuwamy, tym mniej musimy go nawiać i poddać obróbce termicznej.
- Poprawa Komfortu Akustycznego: Praca wentylatorów z niższą prędkością obrotową oznacza znaczące obniżenie poziomu hałasu w kuchni, co bezpośrednio przekłada się na lepsze warunki pracy personelu.
- Wydłużenie Żywotności Komponentów: Mniejsze obciążenie wentylatorów i innych elementów systemu (np. filtrów, nagrzewnic, chłodnic) w okresach niskiego zapotrzebowania może przyczynić się do wydłużenia ich żywotności i zmniejszenia częstotliwości awarii.
Przegląd Dostępnych Technologii i Systemów
Rynek oferuje różnorodne systemy DCKV, różniące się zastosowanymi czujnikami, algorytmami sterowania i stopniem zaawansowania. Niektórzy producenci, jak Halton ze swoim systemem M.A.R.V.E.L., oferują rozwiązania potrafiące sterować przepływem powietrza niezależnie dla każdego okapu lub strefy wentylacyjnej, co dodatkowo zwiększa potencjał oszczędności w dużych kuchniach. Inne systemy, jak Melink Intelli-Hood, wykorzystują algorytmy samouczące się, aby zoptymalizować pracę wentylacji do specyfiki danej kuchni. Firmy takie jak Gaylord Ventilation, EcoAzur czy KlimaGlobal również oferują zaawansowane systemy DCKV, często z dodatkowymi funkcjami monitorowania i zarządzania. Wybór konkretnego systemu powinien być podyktowany specyfiką obiektu, budżetem oraz oczekiwanym poziomem funkcjonalności.
Integracja z IoT i BMS
Nowoczesne systemy DCKV coraz częściej oferują możliwości integracji z szerszymi systemami zarządzania budynkiem (Building Management Systems – BMS) oraz platformami Internetu Rzeczy (Internet of Things – IoT). Taka integracja otwiera drogę do:
- Zdalnego Monitorowania: Śledzenie parametrów pracy systemu (przepływy powietrza, zużycie energii, stan czujników) w czasie rzeczywistym z dowolnej lokalizacji.
- Zdalnego Zarządzania: Możliwość wprowadzania zmian w ustawieniach systemu, harmonogramach pracy itp.
- Raportowania: Generowanie szczegółowych raportów dotyczących zużycia energii, czasu pracy, potencjalnych oszczędności.
- Diagnostyki i Konserwacji Predykcyjnej: System może informować o potencjalnych problemach (np. awaria czujnika, konieczność czyszczenia filtrów) zanim doprowadzą one do poważniejszej awarii, umożliwiając zaplanowanie działań serwisowych.
Aspekty Wdrożeniowe
Decyzja o wdrożeniu systemu DCKV wiąże się z koniecznością poniesienia początkowych kosztów inwestycyjnych, które są wyższe niż w przypadku tradycyjnych systemów. Jednakże, wysoki potencjał oszczędności energii sprawia, że okres zwrotu z inwestycji (ROI) jest często bardzo atrakcyjny, wynosząc zazwyczaj od kilku miesięcy do kilku lat, w zależności od skali obiektu, cen energii i intensywności użytkowania kuchni. Kluczowe dla osiągnięcia sukcesu jest wybranie odpowiedniego systemu oraz zapewnienie jego profesjonalnej instalacji, konfiguracji i uruchomienia przez wykwalifikowanych specjalistów.
Podsumowując, systemy Wentylacji Sterowane Zapotrzebowaniem (DCKV) reprezentują przyszłość wentylacji w kuchniach przemysłowych i innych obiektach o zmiennym obciążeniu. Ich zdolność do inteligentnego dostosowywania pracy do rzeczywistych potrzeb przekłada się na bezprecedensowe oszczędności energii, poprawę komfortu pracy i możliwość zaawansowanego zarządzania systemem, czyniąc je inwestycją, którą zdecydowanie warto rozważyć.
Zaawansowana Filtracja: Czyste Powietrze i Bezpieczeństwo
Podczas gdy tradycyjne filtry przeciwtłuszczowe, takie jak filtry labiryntowe czy siatkowe, stanowią pierwszą linię obrony przed większymi cząstkami tłuszczu, ich skuteczność w wychwytywaniu drobniejszych aerozoli tłuszczowych, dymu oraz neutralizacji zapachów jest ograniczona. Wymagania dotyczące jakości powietrza wywiewanego, bezpieczeństwa pożarowego oraz komfortu (zarówno wewnątrz, jak i na zewnątrz obiektu) skłaniają do poszukiwania bardziej zaawansowanych technologii filtracji. Dwie z nich, które zyskują na popularności w nowoczesnych systemach wentylacji przemysłowej, to filtry elektrostatyczne (ESP) oraz technologia wykorzystująca promieniowanie ultrafioletowe (UV-C).
Filtry Elektrostatyczne (ESP – Electrostatic Precipitators)
Filtry elektrostatyczne działają na zasadzie nadawania ładunku elektrycznego cząstkom zanieczyszczeń (tłuszczu, dymu) przepływającym przez specjalną sekcję jonizującą, a następnie wychwytywania tych naładowanych cząstek na uziemionych płytach kolektora. Dzięki temu mechanizmowi, ESP charakteryzują się bardzo wysoką skutecznością w usuwaniu nawet bardzo drobnych cząstek (aerozoli), których nie są w stanie zatrzymać tradycyjne filtry mechaniczne. Jak wskazują dane producentów (np. DR. AIRE, Klean ESP), efektywność filtracji ESP może sięgać nawet 90-95%.
Zalety filtrów ESP:
- Wysoka skuteczność filtracji: Skuteczne usuwanie dymu i drobnych cząstek tłuszczu.
- Redukcja emisji: Znaczące zmniejszenie ilości zanieczyszczeń emitowanych do atmosfery.
- Ochrona kanałów wentylacyjnych: Mniej tłuszczu osadza się w kanałach, co zmniejsza ryzyko pożaru i potrzebę ich częstego czyszczenia.
- Możliwość integracji: Filtry ESP mogą być zintegrowane bezpośrednio z konstrukcją okapu (np. DR. AIRE, Boton Air), co pozwala zaoszczędzić cenną przestrzeń w kuchni.
- Niski opór przepływu: W porównaniu do niektórych filtrów mechanicznych o wysokiej skuteczności, ESP generują stosunkowo niski opór dla przepływającego powietrza, co może przekładać się na niższe zużycie energii przez wentylatory.
Konserwacja ESP: Kluczowym aspektem utrzymania wysokiej skuteczności filtrów ESP jest ich regularne czyszczenie. Na płytach kolektora gromadzą się wychwycone zanieczyszczenia, które muszą być okresowo usuwane. Częstotliwość czyszczenia zależy od intensywności użytkowania kuchni i rodzaju przygotowywanych potraw. Zaniedbanie konserwacji prowadzi do spadku efektywności filtracji i może stwarzać ryzyko pożarowe.
Technologia UV-C (Ultrafiolet)
Technologia UV-C wykorzystuje promieniowanie ultrafioletowe o określonych długościach fali do neutralizacji tłuszczu i zapachów w powietrzu wywiewanym z okapów. Proces ten opiera się na dwóch głównych mechanizmach:
- Fotoliza (długość fali ok. 254 nm): Promieniowanie UV-C o tej długości fali ma zdolność do rozbijania wiązań chemicznych w organicznych cząsteczkach tłuszczu, przekształcając je w prostsze, mniej lepkie substancje (np. wodę, dwutlenek węgla, niewielkie ilości suchego pyłu). Proces ten zachodzi bezpośrednio na powierzchni lamp UV lub w strumieniu powietrza przepływającym wokół nich.
- Ozonoliza (długość fali ok. 185 nm): Niektóre lampy UV-C emitują również promieniowanie o długości fali 185 nm, które w reakcji z tlenem (O2) zawartym w powietrzu generuje ozon (O3). Ozon jest silnym utleniaczem, który skutecznie neutralizuje cząsteczki odpowiedzialne za nieprzyjemne zapachy oraz dalej utlenia pozostałości tłuszczu.
Systemy UV-C są zazwyczaj instalowane wewnątrz okapu, za filtrami przeciwtłuszczowymi (np. labiryntowymi), aby chronić lampy przed bezpośrednim osadzaniem się grubych warstw tłuszczu.
Korzyści z technologii UV-C:
- Skuteczna kontrola zapachów: Neutralizacja związków zapachowych znacząco redukuje uciążliwość emisji na zewnątrz budynku, co jest szczególnie ważne w gęstej zabudowie miejskiej.
- Redukcja osadów tłuszczu w kanałach: Rozkładanie tłuszczu przez UV-C zapobiega jego gromadzeniu się w kanałach wentylacyjnych, co drastycznie zmniejsza ryzyko pożaru i wydłuża okresy między czyszczeniami kanałów.
- Poprawa higieny: Promieniowanie UV-C ma również właściwości bakteriobójcze i wirusobójcze.
- Współpraca z innymi filtrami: UV-C może skutecznie uzupełniać działanie filtrów mechanicznych i ESP.
- Systemy samoczyszczące: Niektóre okapy z technologią UV-C są wyposażone w systemy automatycznego mycia wodą (np. Streivor), co dodatkowo ułatwia konserwację.
Bezpieczeństwo i Konserwacja UV-C: Należy pamiętać, że bezpośrednia ekspozycja na promieniowanie UV-C jest szkodliwa dla oczu i skóry. Systemy muszą być wyposażone w odpowiednie zabezpieczenia (np. wyłączniki krańcowe), uniemożliwiające pracę lamp przy otwartym okapie lub podczas prac serwisowych. Generowanie ozonu (przy lampach 185 nm) również wymaga uwagi – jego stężenie w powietrzu musi być kontrolowane, aby nie przekraczało dopuszczalnych norm. Lampy UV-C mają ograniczoną żywotność i wymagają okresowej wymiany zgodnie z zaleceniami producenta.
Systemy Hybrydowe i Filtry z Węglem Aktywnym
Dla najbardziej wymagających zastosowań, gdzie konieczna jest maksymalna redukcja zarówno cząstek stałych, jak i zapachów, stosuje się systemy hybrydowe, łączące zalety różnych technologii, najczęściej ESP i UV-C (np. DR. AIRE, Airwave). Takie połączenie pozwala na kompleksowe oczyszczenie powietrza wywiewanego.
W niektórych przypadkach, szczególnie w systemach z częściową recyrkulacją powietrza lub tam, gdzie wymagania dotyczące neutralizacji zapachów są ekstremalnie wysokie, jako ostatni stopień filtracji stosuje się filtry z węglem aktywnym. Węgiel aktywny, dzięki swojej porowatej strukturze, adsorbuje cząsteczki zapachowe. Filtry te wymagają jednak regularnej wymiany złoża węglowego, co generuje dodatkowe koszty eksploatacyjne.
Wybór odpowiedniej technologii zaawansowanej filtracji zależy od specyfiki obiektu, rodzaju prowadzonej działalności, lokalnych przepisów dotyczących emisji oraz dostępnego budżetu. Inwestycja w ESP lub UV-C, choć początkowo droższa, często zwraca się poprzez niższe koszty czyszczenia kanałów, zwiększone bezpieczeństwo pożarowe oraz eliminację problemów związanych z uciążliwością zapachową.
Wdrożenie Optymalizacji: Krok po Kroku
Decyzja o modernizacji i optymalizacji systemu wentylacji przemysłowej to strategiczny krok, który przynosi długoterminowe korzyści. Aby jednak proces ten przebiegł sprawnie i przyniósł oczekiwane rezultaty, warto podejść do niego w sposób metodyczny. Poniżej przedstawiamy kluczowe etapy wdrażania optymalizacji systemu wentylacji.
Etap 1: Ocena Istniejącego Systemu (Audyt)
Pierwszym i fundamentalnym krokiem jest dokładna ocena stanu obecnego systemu wentylacyjnego. Profesjonalnie przeprowadzony audyt pozwoli zidentyfikować słabe punkty, obszary o największym potencjale poprawy oraz określić punkt wyjścia do dalszych działań. Audyt powinien obejmować:
- Analizę techniczną: Sprawdzenie stanu technicznego wszystkich komponentów systemu – okapów, filtrów, wentylatorów, kanałów wentylacyjnych, elementów automatyki. Ocena stopnia zużycia, ewentualnych uszkodzeń czy nieszczelności.
- Pomiary wydajności: Zmierzenie rzeczywistych przepływów powietrza w kluczowych punktach systemu i porównanie ich z wartościami projektowymi oraz aktualnymi potrzebami.
- Audyt energetyczny: Analiza zużycia energii przez poszczególne elementy systemu, w szczególności wentylatory. Identyfikacja największych „pożeraczy” energii.
- Ocenę skuteczności: Weryfikacja, czy obecny system skutecznie usuwa zanieczyszczenia (dym, parę, zapachy) i zapewnia odpowiednie warunki pracy (komfort termiczny, poziom hałasu).
- Analizę zgodności z przepisami: Sprawdzenie, czy system spełnia aktualne normy i wymagania prawne dotyczące wentylacji, bezpieczeństwa pożarowego i emisji zanieczyszczeń.
Wyniki audytu stanowią podstawę do podjęcia decyzji o zakresie i kierunku modernizacji.
Etap 2: Identyfikacja Obszarów do Poprawy i Planowanie Modernizacji
Na podstawie wyników audytu należy zidentyfikować konkretne działania optymalizacyjne. Mogą one obejmować:
- Wymianę wentylatorów: Zastąpienie starych, nieefektywnych wentylatorów nowymi modelami o wysokiej sprawności (np. z silnikami EC).
- Instalację napędów VSD/VFD: Dodanie przemienników częstotliwości do istniejących wentylatorów w celu umożliwienia regulacji ich prędkości.
- Wdrożenie systemu DCKV: Instalacja czujników i sterownika systemu wentylacji sterowanej zapotrzebowaniem.
- Modernizację systemu filtracji: Wymiana standardowych filtrów na bardziej zaawansowane (np. ESP, UV-C) lub dodanie dodatkowych stopni filtracji.
- Instalację systemu odzysku ciepła: Dodanie rekuperatora w celu odzyskiwania energii z powietrza wywiewanego.
- Uszczelnienie lub modernizację kanałów wentylacyjnych: Eliminacja nieszczelności, optymalizacja przebiegu kanałów w celu zmniejszenia oporów przepływu.
Kolejnym krokiem jest planowanie modernizacji. Na tym etapie należy:
- Dobrać odpowiednie technologie: Wybrać konkretne urządzenia i systemy, które najlepiej odpowiadają zidentyfikowanym potrzebom i specyfice obiektu.
- Przeprowadzić analizę kosztów i korzyści (ROI): Oszacować koszty inwestycyjne związane z zakupem i instalacją nowych technologii oraz przewidywane oszczędności eksploatacyjne (energia, konserwacja), aby ocenić opłacalność inwestycji i okres zwrotu.
- Przygotować projekt techniczny: Opracować szczegółowy projekt modernizacji, uwzględniający wszystkie aspekty techniczne i instalacyjne.
- Wybrać wykonawcę: Zlecić realizację prac doświadczonej firmie specjalizującej się w systemach wentylacji przemysłowej.
Etap 3: Realizacja Modernizacji i Uruchomienie
Ten etap obejmuje fizyczną instalację nowych komponentów systemu zgodnie z projektem technicznym. Kluczowe jest zapewnienie prawidłowego montażu, podłączenia i konfiguracji wszystkich urządzeń, szczególnie systemów sterowania (DCKV, VSD) i czujników. Po zakończeniu prac instalacyjnych następuje faza uruchomienia i regulacji systemu, która ma na celu sprawdzenie poprawności działania wszystkich elementów i optymalne dostrojenie parametrów pracy (np. progów zadziałania czujników DCKV, krzywych regulacji VSD).
Etap 4: Znaczenie Regularnej i Profesjonalnej Konserwacji
Optymalizacja systemu wentylacyjnego to nie jednorazowe działanie, lecz proces ciągły. Aby utrzymać wysoką efektywność energetyczną i niezawodność zmodernizowanego systemu przez długie lata, niezbędna jest regularna i profesjonalna konserwacja. Obejmuje ona wszystkie czynności wymienione przy omawianiu efektywności energetycznej, ze szczególnym uwzględnieniem specyfiki nowych technologii:
- Czyszczenie filtrów ESP: Zgodnie z zaleceniami producenta i intensywnością użytkowania.
- Wymiana lamp UV-C: Po upływie ich żywotności.
- Przeglądy i kalibracja czujników DCKV: Zapewnienie ich prawidłowego działania.
- Kontrola pracy VSD i silników EC.
- Czyszczenie wymienników ciepła w rekuperatorach.
Zaleca się opracowanie szczegółowego harmonogramu konserwacji i powierzenie jej wykonywania wyspecjalizowanej firmie serwisowej. Regularne przeglądy pozwalają nie tylko utrzymać system w optymalnej kondycji, ale również wcześnie wykrywać potencjalne problemy, zapobiegając kosztownym awariom.
Prawidłowo przeprowadzone wdrożenie optymalizacji, obejmujące wszystkie powyższe etapy, gwarantuje, że inwestycja w nowoczesne technologie wentylacyjne przyniesie maksymalne korzyści i będzie służyć niezawodnie przez wiele lat.
Podsumowanie: Inwestycja w Przyszłość Kuchni
Optymalizacja systemu wentylacji przemysłowej to już nie luksus, lecz strategiczna konieczność dla każdego nowoczesnego obiektu gastronomicznego czy zakładu produkcyjnego. Jak wykazano w niniejszym artykule, inwestycja w zaawansowane technologie, takie jak wysokosprawne wentylatory z silnikami EC, napędy o zmiennej prędkości (VSD), inteligentne systemy sterowania zapotrzebowaniem (DCKV) oraz nowoczesne metody filtracji (ESP, UV-C), przynosi szereg wymiernych korzyści, które wykraczają daleko poza samo zapewnienie czystego powietrza.
Przede wszystkim, oszczędności finansowe są najbardziej namacalnym efektem optymalizacji. Drastyczna redukcja zużycia energii elektrycznej przez wentylatory oraz zmniejszenie zapotrzebowania na energię do ogrzewania lub chłodzenia powietrza uzupełniającego przekładają się na znaczące obniżenie rachunków za energię. W dobie rosnących kosztów operacyjnych, efektywność energetyczna staje się kluczowym czynnikiem konkurencyjności.
Po drugie, poprawa warunków pracy personelu jest nie do przecenienia. Cichsza praca systemu wentylacyjnego dzięki DCKV i VSD, stabilniejsze warunki termiczne oraz wyższa jakość powietrza w pomieszczeniach bezpośrednio wpływają na komfort, zdrowie i wydajność pracowników.
Po trzecie, zgodność z normami i przepisami staje się łatwiejsza do osiągnięcia. Nowoczesne systemy wentylacyjne, szczególnie te wyposażone w zaawansowaną filtrację, pozwalają na spełnienie coraz bardziej rygorystycznych wymagań dotyczących emisji zanieczyszczeń i zapachów, a także norm bezpieczeństwa pożarowego.
Wreszcie, mniejszy wpływ na środowisko naturalne to aspekt coraz bardziej istotny zarówno z punktu widzenia odpowiedzialności społecznej biznesu, jak i wizerunku firmy. Redukcja zużycia energii oznacza mniejszą emisję gazów cieplarnianych i bardziej zrównoważoną działalność.
Rekomendujemy, aby technologie optymalizacyjne były brane pod uwagę na każdym etapie inwestycji – zarówno podczas projektowania nowych obiektów, jak i przy planowaniu modernizacji istniejących instalacji. Choć początkowy koszt wdrożenia może być wyższy, długoterminowe korzyści w postaci niższych kosztów eksploatacyjnych, większej niezawodności i lepszego środowiska pracy sprawiają, że jest to inwestycja, która szybko się zwraca i procentuje w przyszłości.
Przyszłość wentylacji przemysłowej rysuje się w kierunku dalszej integracji inteligentnych systemów, wykorzystania sztucznej inteligencji (AI) do jeszcze bardziej precyzyjnej optymalizacji pracy, rozwoju nowych, jeszcze skuteczniejszych i bardziej energooszczędnych materiałów filtracyjnych oraz coraz większego nacisku na zrównoważony rozwój. Świadome podejście do optymalizacji systemów wentylacyjnych to inwestycja nie tylko w efektywność operacyjną, ale przede wszystkim w przyszłość bezpiecznej, komfortowej i odpowiedzialnej działalności.
0 komentarzy